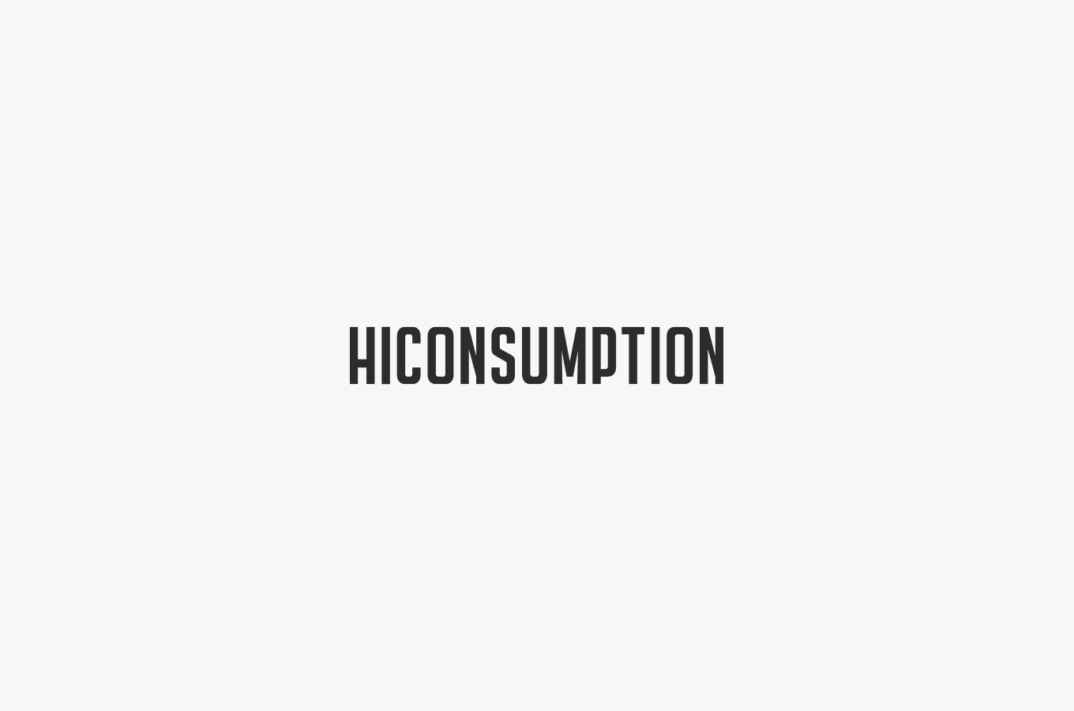
Tucked in the upper region of northwestern Pennsylvania, hugging the outskirts of the Allegheny National Forest just south of the NY state line is the quintessentially small town of Bradford. The closest major city, Buffalo, resides nearly 78 miles due north making this sleepy yet incredibly charming town a quiet reprieve from today’s urban hustle and bustle. Moreover, alongside its picturesque interior northeastern scenery – painted bright red and orange during the fall months – is another fiery resident that’s held its own as an American legacy brand for 85 years.
Since 1932, the Zippo Manufacturing Company has built American-made windproof lighters for American tobacco enthusiasts, the American military, or anyone interested in keeping a reliable flame at the ready. Everything about the brand is strictly Americana where, even today, each and every one of their 12 million lighters manufactured per year is hand inspected for quality control every step of the way. It’s a miraculous means of wedding both man and machine – enabling Zippo to ship their lighters across the nation and the world with a lifetime guarantee. Interested in seeing the process for yourself? Take a peek inside the Zippo manufacturing plant below.
Like all products, each Zippo lighter begins its life as a concept that’s later designed in conjunction with current trends in the market. These designs are then approved by their seasoned R&D team and pushed into production. From here, the first tangible piece of the puzzle begins with the case fabrication, where Zippo lighter cases are stamped from brass and hinges formed from stainless steel. The two metals are then welded together, buffed and then polished for a perfect shine.
On any given day, Zippo manufactures roughly 70k lighters for market – that’s approximately 12 million per year.
After polishing, the newly formed cases begin the plating step of the process. Here, each of the brass cases are coated in nickel – since chrome doesn’t adhere directly to brass metals. After, each lighter then goes through a series of rinses prior to entering a chrome solution for four minutes. They’re then loaded onto plating racks and removed by hand. On a regular day, Zippo can plate up to 3,400 lighter cases an hour.
A key part of the process at this point is known as the “fit-up” stage. This is where each lighter is matched with the appropriate fittings. Anyone who’s owned a Zippo knows that these fittings are removable – necessary for refilling the lighters with fluid – so it’s at this stage where two key elements of the Zippo lighter become one.
Also, workers at this stage verify a key element of any Zippo lighter – the trademark Zippo “click” you hear when opening the case. Sounds tedious we know, but it’s little details such as this that work to add a level of nostalgia and brand recognition across the board.
VP of Operations: Tim VanHorn
In terms of the manufacturing process, what sets Zippo apart from the competition?
Our wide variety of decorating and design processes are unmatched by any other lighter manufacturer. What started as a time consuming engraving and hand-painting process, has evolved into laser engraving and full-photo replication with our color imaging process, with even more innovative decorating techniques on the horizon.
What is it about the Zippo brand that has such high retainment of employees – in some cases 50+ years?
Zippo ownership is deeply committed to their employees and the community of Bradford, PA. There is a big element of hometown pride at Zippo – it’s an honor to make a product that is recognized and purchased around the world.
How would you define an American legacy brand and what is it about American manufacturing that sets our products above the fray of international competition?
Zippo has remained true to our roots over the past 85 years…there are some manufacturing process steps, such as buffing the lighter to a mirror shine, and testing for the famous Zippo click, that are still best done by hand by our highly skilled team. As the company continues to diversify, our outdoor and lifestyle products will all align with the heritage and iconic American style Zippo founded with the windproof lighter.
As far as brand diversity is concerned, Zippo – with its seemingly endless collection of various art and engravings on their windproof lighters – is one of the best in the business. And it’s the next step in the process – decoration – that help sets each lighter apart in their own way. In this stage, potential finishes include powder coating, Softtouch design coating, emblems, various engravings, or epoxy and rhinestone inlays.
Each of their 12 million lighters manufactured per year is personally hand inspected for quality control every step of the way.
To achieve these finishes, Zippo lighters are sent through a closed-door color imaging room where a protected machine applies the color design and then moves the customized lighters toward an inspection area. Once again, each lighter is checked by hand to ensure there were no errors made during the decoration process.
After color is applied, these newly decorated lighters are then moved onto the computer engraving stage of the manufacturing process. At this point, lighter cases are either machine or laser engraved utilizing proprietary Zippo technology. A bit illusive in nature, it’s here where your Zippo lighter really comes to life – developing a personality all of its own.
Later, necessary component parts of the lighters such as the wick, flint, cam and spark wheel are added to the newly finished unit. Also, cotton is then placed inside the fuel chamber from the bottom while a felt pad and flint screw round out the lighter insert for full functionality.
The completed lighters are then transported to the packaging area where a warning label is then added before they’re boxed in shipping cartoons that house up to 2,500 lighters at a time. These boxes are then shipped to distributors around the globe – contributing to the 565 million+ lighters ever built and shipped out of the original Bradford, PA facility.
Functioning as familial heirlooms or reliable lifelong everyday carry items, its evident that Zippo lighters are a true testament to American ingenuity and dedication to building quality products right here on our own soil. And while some aspects of the manufacturing process have changed over the years to match demand, it’s evident Zippo isn’t interested in cutting corners in their production – allowing for the quality of their products to speak for themselves.
© Photography by HiConsumption
Finished Product: Zippo 1935 Replica Original
Nothing beats an original. Especially knowing the effort involved to make such a staple piece, there’s certainly a newfound appreciation for these classic lighters. This USA-made 1935 Replica, for instance, comes complete with a brushed chrome finish, all metal windproof construction, and of course Zippo’s lifetime guarantee.